Sections
Establishing and maintaining buffer zones as additional space between the community and hazardous operations or chemical storage is an essential consideration for risk management.
Incidents such as the 2013 West Fertilizer Company and the 2015 Tianjin, China explosions demonstrate why it is crucial to maintain adequate buffer zones between hazardous chemicals and the community. A buffer zone is an expanse of land that separates hazardous operations and chemicals from public receptors (e.g., homes, schools, and hospitals).
As part of a set of risk mitigation measures, it is vital that manufacturers site new operations with adequate buffer zones between industry and the community, as well as maintain and improve buffer zones at existing facilities. Additionally, it is critical that the chemical industry partners with government agencies to ensure that existing buffer zones are not compromised due to local development.
This article discusses why buffer zones are important to establish and maintain around chemical processing facilities. It introduces the buffer zone requirements that one chemical company has implemented to protect local communities around operational sites.
Past incidents necessitate buffer zones
Many incidents involving chemical processing facilities and storage sites have confirmed the importance of land use planning. One such incident is the 2013 West Fertilizer Company (WFC) fire and explosion that resulted in 15 fatalities and over 260 injured (1). When the fertilizer facility was first built in 1962, primarily open fields surrounded the facility. Over the years, the city of West, TX, encroached closer and closer to the WFC facility. This encroachment ultimately led to the significant amount of destruction associated with the 2013 explosion.
The blast caused the complete destruction of a 22-unit apartment complex (450 ft from the explosion), a 145-bed nursing home (500 ft from the explosion), an intermediate school (552 ft from the explosion), and a high school (1,263 ft from the explosion). The explosion destroyed around 70 residential homes and damaged approximately 60 more.
In 2006, an explosion fueled by vapor released from a 2,000-gal tank of highly flammable liquid at the CAI/Arnel manufacturing facility rocked the town of Danvers, MA (2). The explosion and subsequent fire heavily damaged dozens of nearby homes and businesses; 24 homes and six businesses were damaged beyond repair. Fortunately, since the incident occurred at 2:40 AM, most of the home occupants were in their beds covered with blankets, which protected them from flying glass and other debris. In total, only ten people were injured. It is likely that fatalities could have resulted had the explosion occurred during the daytime.
Much like the WFC incident, the population gradually encroached closer to the CAI/Arnel facility in the years leading up to the explosion. Over several decades, the peninsula where the CAI/Arnel facility was located transitioned from a sparse population to one with many residential homes. Some homes were only 150 ft away from the facility. During the same period, the facility transitioned from handling a few hundred gallons of flammable liquids to thousands of gallons.
Another catastrophic incident occurred in August 2015 at the Port of Tianjin, China (3, 4). A series of explosions at a container storage station resulted in 173 fatalities, and hundreds of people were injured. The explosion forced several thousand people living near the port to leave their homes and seek refuge elsewhere.
All three incidents are similar in that there was a lack of proper land use planning. In West, TX, there were no zoning regulations requiring residential areas to be separated from the fertilizer facility. In Tianjin, there was a requirement that prohibited public buildings and facilities within 3,300 ft of the container station. However, the requirements for separation in Tianjin were not followed, and at least three major residential communities were located within this perimeter. In Danvers, MA, property licensing laws and regulations did not address storing or using toxic chemicals.
A more recent explosion which speaks to the dangers of allowing dense populations near hazardous chemicals occurred in August 2020 at the Port of Beirut, Lebanon (5). A series of explosions, caused by ammonium nitrate that had been stored for six years at a warehouse in the port, resulted in 220 fatalities and injured more than 6,500 people. The nearby dense residential and commercial areas were severely damaged, leaving ~300,000 people homeless. Additionally, this disaster damaged nine of the capital’s hospitals and hampered access to healthcare for nearly 160,000 patients.
The Dow Chemical Company Greenbelt Standard
The Dow Chemical Company (Dow) has implemented a standard set of buffer zone (i.e., greenbelt land) requirements to protect the communities located near our operating facilities. The five requirements of the Greenbelt Standard are:
- Review projects and new facilities. Projects (e.g., construction of a new facility or expansion of an existing facility) that result in off-site impacts are reviewed by upper-level leadership.
- Maintain land around existing facilities. Greenbelt land around the site must be maintained to minimize the risk to the community and to limit community exposure to hazardous chemicals, in addition to other protection layers to manage hazards.
- Develop site-specific land use strategies. Sites with potential off-site impact scenarios should develop and maintain a land use strategy for land within the impacted area. The land use strategy summarizes the potential offsite impacts that a site can pose and details the land owned by the company. In addition, it lists potential areas of acquisition so that the buffer zone can be expanded if desired. The land use strategy also places restrictions on the use of the buffer zone land itself to prevent increasing the risk to the community.
- Conduct land transaction reviews. Transactions involving land impacted by Dow operations are reviewed and approved by process safety and upper-level leadership.
- Evaluate new owners or tenants. Prior to selling or leasing land to other chemical or petrochemical operators, the proposed company is evaluated to determine if they meet fundamental process safety management principles. The proposed owner/tenant is expected to identify any potential impacts from their operations beyond their facility boundaries. If their operations can impact Dow facilities, or if our hazards can impact their operations, the proposal is reviewed and approved by upper-level leadership.
History of the Greenbelt Standard
In 2011, senior leadership within Dow requested a formal protocol for managing buffer zones around our operations. Dow issued the protocol in 2012 as a company guidance document. After the WFC explosion in 2013, Dow leadership decided to strengthen the protocol by making the Greenbelt Standard a mandatory standard for all Dow operations. The guidance was re-issued as a formal standard in 2014. Prior to the Greenbelt Standard, land use for capital projects and changes to our greenbelt areas were managed at the site level using the management of change work process. The Greenbelt Standard required higher-level reviews and approvals as well as the standardization of the key considerations used to evaluate potential land transactions and facility changes with potential off-site impacts.
When the Greenbelt Standard was implemented in 2014, broad training was offered within Dow to communicate the new requirements. Land use strategies were developed for all sites with the potential to have off-site impacts. These strategies included plans for existing greenbelt land and any potential expansion of the buffer zone.
Drive for continuous improvement
Since implementing the 2014 Greenbelt Standard, we have learned a great deal. As a result, in 2019, the standard was updated and re-issued.
The need for clarification and consistency was the first main driver for updating the standard. Changes related to clarification and consistency included:
- Consistent criteria for calculating extent distances for potential off-site impacts were established.
- Expectations for leaders of Dow facilities operating within a non-Dow owned industrial park (iPark) were established; leaders are now expected to notify iPark leadership of any hazards from Dow operations that may extend beyond the iPark site perimeter.
- A minimum revalidation/update frequency for each site’s land use strategy was determined.
The need for greater transparency in documentation and required representation was the second key driver for updating and re-issuing the Greenbelt Standard. Changes were made to the standard such that each site’s land use strategy must now include required documentation of the maximum extent distances for potential hazard impacts from the site and the potential off-site population that could be impacted. In addition, when developing or revalidating land use strategies, process safety, emergency services, and security personnel must be represented.
Although we wanted to ensure consistency in endpoint distance calculations, we allow facility safety managers to use the process safety tools they prefer to estimate those distances (in an effort to reduce non-value-added work). With this approach, most facilities were able to refer to existing process hazard analysis studies and did not have to perform new calculations. Some of the typical modeling tools we use include DNV’s PHAST software, Baker Risk’s SafeSite3G software, and the Risk Analysis Screening Tool (RAST) originally created by Dow, which is now publicly available via the Center for Chemical Process Safety (CCPS).
After the Greenbelt Standard was updated, a broad communication was sent to impacted leaders and supplemental training opportunities were offered. Additionally, all site leaders received an action to report progress on achieving compliance with the standard such that progress could be monitored at a corporate level.
Program results
The land use strategy documentation requirement proved to be an effective way to ensure thoughtful consideration of hazards and the potential impact those hazards could have on the surrounding community. Since the original 2012 issue of guidance on greenbelt management, some notable achievements include:
- Off-site impacts were estimated for more than 100 sites and land use strategies were developed as needed.
- Leadership at many of our sites began advocating for land use planning within local forums. For example, Dow successfully advocated against a charter school development that was proposed to be located near our operations. As a result, the school permit was denied.
- Additional land has been acquired to improve buffer zones at 16 of our sites.
- Conservation sales or donations have occurred for land near four of our sites. This allows the land to serve as an open space and preserves the space as a natural habitat.
- Well over 130 proposed land transactions have received process safety reviews. In some cases, otherwise economically advantageous transactions were rejected due to process safety concerns.
Program partnership
As part of Dow’s 2025 sustainability goals, Dow committed to a business decision process that values nature (6). This commitment delivers business value and natural capital value through projects that are good for business and ecosystems. Specialized tools were developed with The Nature Conservancy nonprofit for this purpose; these tools provide the data needed to assess the value provided by the ecosystem and compare it with alternatives. This allows us to make business decisions that take nature into account.
In 2017, the team responsible for the Greenbelt Standard formed a partnership with Dow’s “Valuing Nature” team. As a result, we use the valuing nature evaluation protocol to screen all greenbelt real estate acquisitions to identify opportunities for engineered solutions that provide co-benefits for the environment. Some examples where we have benefited the environment through our use of our buffer zones include:
- constructed wetlands (Figure 1). To meet suspended solids requirements for wastewater treatment, a constructed wetland was installed instead of a more traditional sequencing batch reactor (7). The lifecycle assessment of both options indicated that the lower energy and material inputs to the constructed wetland would yield lower potential environmental impacts. These include fossil fuel use, acidification, smog formation, and ozone depletion that likely lead to lower potential impacts for global warming and marine eutrophication.
- drying ponds. To allow recycling of filtered water, drying ponds were installed within a buffer zone. The drying ponds increased water supply resiliency for the site and reduced freshwater intensity and demand on the nearby river basin.
- sustainable land management. To enhance bio-diversity while also lowering operating and maintenance costs, land intervention, such as mowing, was scheduled based on safety and access needs. Land that did not require periodic access was used for habitat creation and installation of native species.
- land conservation. To prevent settlement of buffer zone land, some land was divested and placed in conservation through sale or lease.
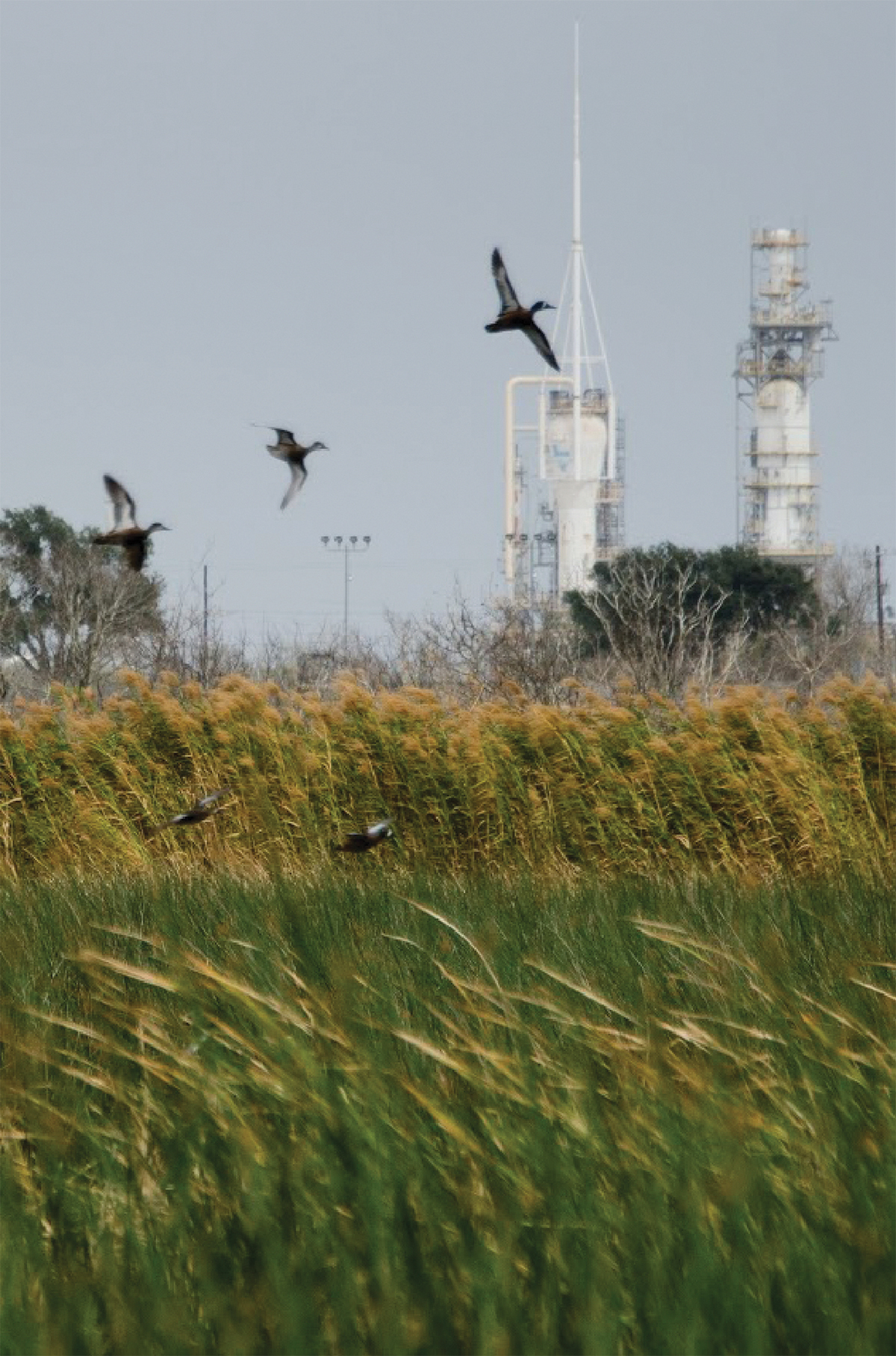
▲Figure 1. The constructed wetlands within the buffer zone area of an operating facility were used to meet requirements for wastewater treatment instead of a more traditional sequencing batch reactor.
Effective greenbelt management case studies
To illustrate greenbelt management practices, three case studies are detailed. The specific case studies utilize generic names but reflect true accounts of how the work process has been applied to effectively manage greenbelt areas.
Study 1. Dowville. The Dowville site handles flammable and toxic chemicals, and multiple protection layers are in place to prevent inadvertent releases. However, in a worst-case scenario, the impact could extend up to 820 ft, as shown in Figure 2. There is adequate greenbelt space to the east of the facility to prevent community impact, but there is a potential to impact industrial neighbors to the west and south.
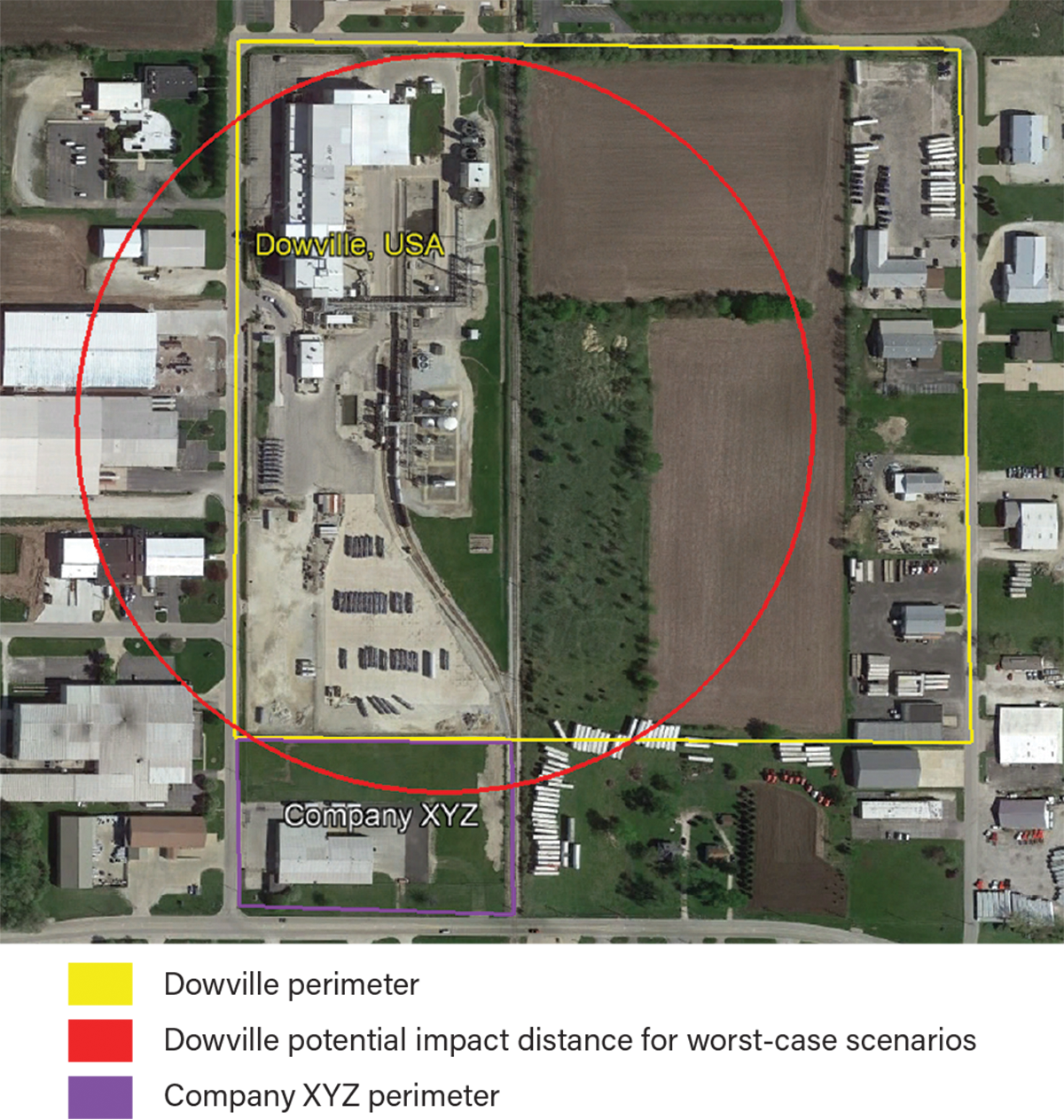
▲Figure 2. The Dowville site managed to purchase land that falls within their potential impact area, further increasing their greenbelt buffer zone.
Following Dow’s Corporate Greenbelt Standard, a land use strategy was developed for the site. As part of Dowville’s land use strategy, a local real estate firm was engaged to monitor for purchase opportunities within the potential impact area. In 2017, the real estate firm notified site leadership of an opportunity; the industrial neighbor to the south, Company XYZ, was relocating operations and placed their property on the market. The property was approximately five acres and included a 25,000-ft2 building. Although a local paint brush manufacturer was also interested in the property, Dowville managed to win the bid with a purchase price of $500,000, thus increasing their greenbelt to the south. Properties to the west are still monitored for additional greenbelt expansion opportunities.
Study 2. Dow-Crossing. Dow-Crossing is a valve station that handles propane at 1,200 psig. Although this facility has multiple protection layers in place to prevent inadvertent releases, in a worst-case scenario, flammable impacts from Dow-Crossing could extend up to 700 ft (Figure 3). In 2018, Company Astro informed Dow that they were interested in purchasing a portion of the undeveloped land at Dow-Crossing. Company Astro wanted to buy the land indicated in the purple-shaded region in Figure 3 to build a warehouse. The potential impact area from a worst-case scenario, indicated in red, included a portion of the land being evaluated for divestiture. Based on a review of the potential flammable impacts on the land and consistent with Dow’s Corporate Greenbelt Standard, a recommendation was made to not accept the offer. Upper management supported the decision, and the offer was declined.
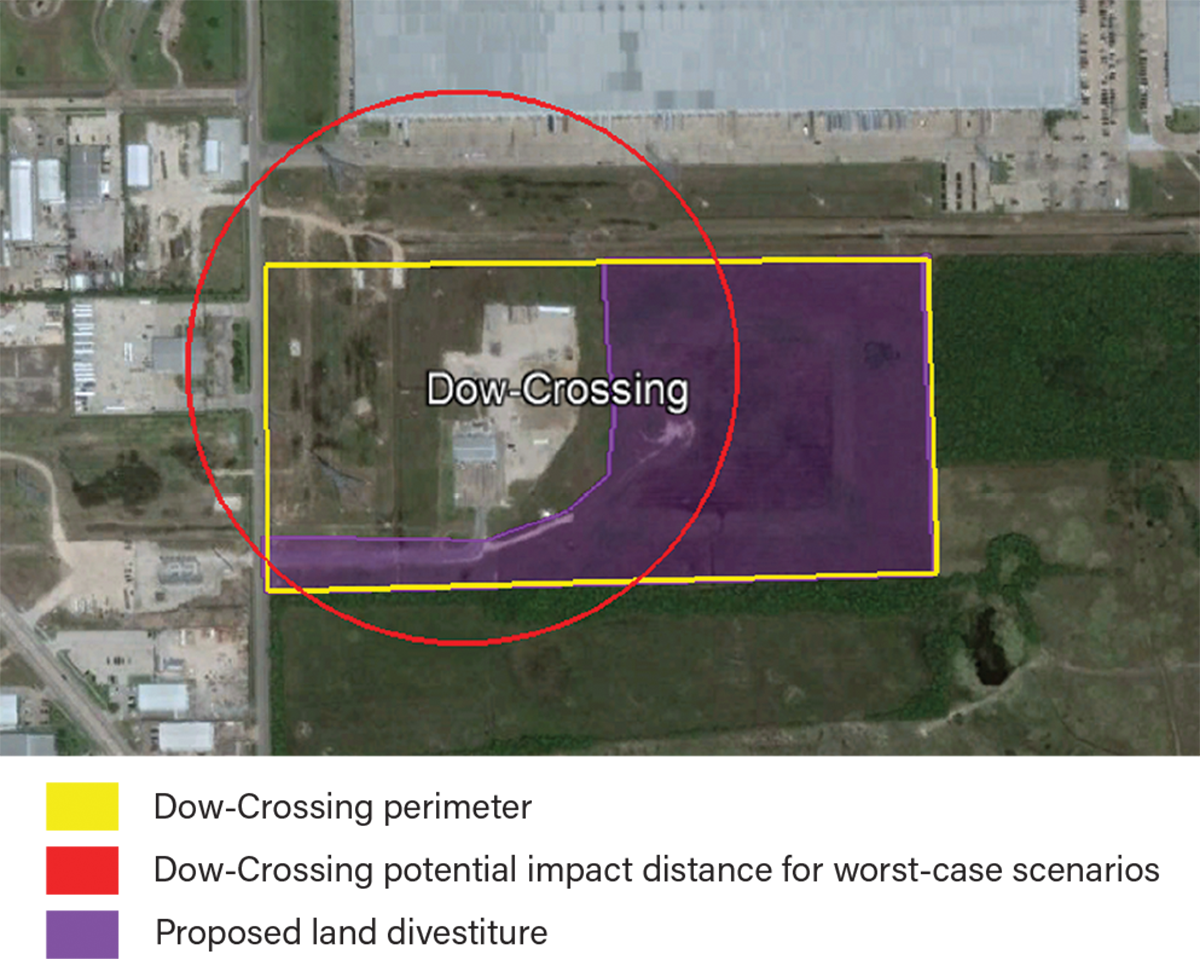
▲Figure 3. An offer was received to purchase a portion of land within Dow-Crossing. Because the proposed land divestiture fell within the potential impact area, Dow declined the offer.
Study 3. Dow Green site. The Dow Green facility purchased some land offsite with the objective of increasing their buffer zone from the community. They are working with a local partner to plant native grasses and trees, thereby creating a pollinator garden (Figure 4). This represented a good opportunity to widen the buffer zone while contributing to nature and creating an improved aesthetic for the community.
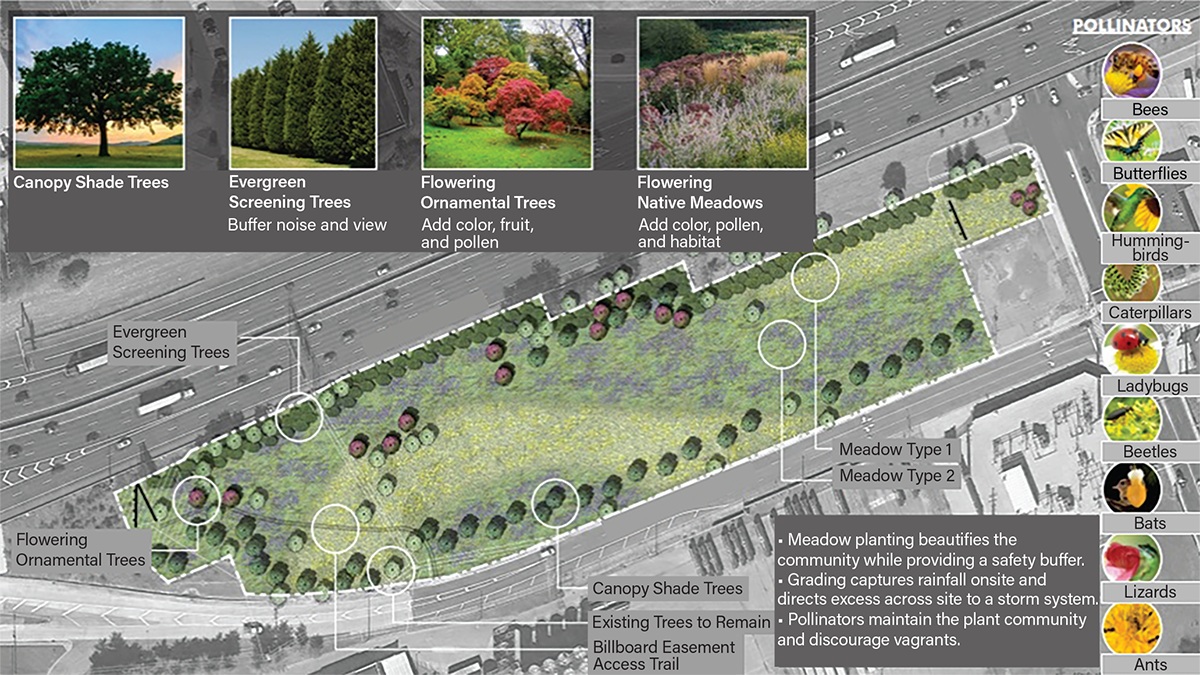
▲Figure 4. The Dow Green site’s pollinator garden highlights the ability to enhance nature within a site’s buffer zone.
Best practices and future improvements
Land use strategies are not static; they are influenced by operational changes on site as well as by changes to land use around the facility. Therefore, facilities are expected to review their strategies at least every four years. Several sites have established standing land use committees that monitor for changes within or outside of the facility that could impact the land use strategy and review and update the strategy more frequently. This is an approach that can be leveraged to increase the effectiveness of the greenbelt program.
A future extension of the greenbelt program will include similar types of reviews and approvals for land and building transactions (leases, property transfers, and sales) within our site boundaries to ensure the application of a consistent approach that adequately manages potential risks. Elements of the Greenbelt Standard are being incorporated within the mergers and acquisitions due diligence work process; this will ensure that a site buffer zone evaluation will occur prior to acquiring assets.
It is also important for the chemical industry — and the surrounding communities — to lobby for land use regulations that enable economic growth while sensibly restricting zoning and limiting new construction close to operating chemical facilities. Dow has successfully lobbied against developments near some of our operations. As mentioned previously, a charter school with outdoor soccer fields was proposed to be built near one of our operating facilities. The proposed location was undeveloped land well within our operations’ potential impact area. Site leadership met with local government officials and made a strong case to only allow industrial development in the area. Agreement was reached and the charter school permit was denied.
Conclusion
It is clear from past incidents that it is vital to maintain adequate separation between industry and the community. Dow’s formal protocol for greenbelt management has served to ensure that the areas around our operations are evaluated, and strategies are created to appropriately manage buffer zones. The requirements of the Greenbelt Standard are straightforward; however, strong support from corporate leadership is key to achieving success from any program of this nature.
While Dow’s program for buffer zone management is a great step toward further limiting the consequences of potential hazard scenarios, more action is required. The approach described in this paper is highly leverageable, and other companies are urged to develop similar approaches to ensure that they maintain adequate separation between potential hazards and the community. It is vital that the chemical industry seek to site new operations with adequate buffer zones between industry and the surrounding community and to proactively maintain and improve existing buffer zones. Additionally, it is critical that companies in the chemical process industries partner with local governments and regulators to ensure that buffer zones are not compromised due to local development and/or lack of regulation.
Literature Cited
- U.S. Chemical Safety and Hazard Investigation Board, “West Fertilizer Company Fire and Explosion,” Investigation Report 2013-02- I-TX, CSB (Apr. 2013).
- U.S. Chemical Safety and Hazard Investigation Board, “Confined Vapor Cloud Explosion,” Investigation Report 2007-03-I-MA, CSB (May 2008).
- Calamur, K., “China’s Response to the Tianjin Explosions,” The Atlantic, www.theatlantic.com/international/archive/2015/08/chinas-response-tianjin-explosions/401426 (Aug. 2015).
- Phillips, T., and F. Ryan, “Tianjin Blasts: China Orders Nationwide Checks on Dangerous Chemicals,” The Guardian, www.theguardian.com/world/2015/aug/14/tianjin-explosions-china-orders-checks-chemicals (Aug. 2015).
- Al-Hajj, S., et al., “Beirut Ammonium Nitrate Blast: Analysis, Review, and Recommendations,” Frontiers in Public Health, 9, #657996 (June 2021).
- Guertin, F., et al., “From Ash Pond to Riverside Wetlands: Making the Business Case for Engineered Natural Technologies,” Science of the Total Environment, 651 (Part 1), pp. 419–426 (Sept. 2018).
- DiMuro, J. L., et al., “A Financial Analysis of Constructed Wetlands for Industrial Wastewater Treatment,” Journal of Industrial Ecology, 18 (5), pp. 631–640 (Apr. 2014).
Copyright Permissions
Would you like to reuse content from CEP Magazine? It’s easy to request permission to reuse content. Simply click here to connect instantly to licensing services, where you can choose from a list of options regarding how you would like to reuse the desired content and complete the transaction.