The primary objectives of effective process safety programs are prevention of fatalities and other injuries, and avoidance of significant property damage and environmental harm to provide overall safe and reliable operations (1, 2). Three key questions should be considered in assessing program performance (3, 4):
1. What is the current level of process safety performance? While it may seem straightforward to assess current performance based on the number of past incidents, serious process safety incidents are generally rare and not a good metric. Performance must therefore typically be assessed in terms of conformance to process safety program requirements and goals. Program goals should include prevention of injuries and incidents, and measurement of the day-to-day effectiveness of process safety program requirements to manage the process hazards present and provide early warning of possible problems. Like medical professionals who measure vital signs such as blood pressure for early warning of potential health problems, appropriate goals and metrics should be established and monitored to provide feedback on current process safety performance.
The current status is important, because if a company already has excellent performance, it should strive to maintain that high level. But if a company or site has poor performance, it should set additional goals and provide resources for improvement.
2. Will performance in the future be better, about the same, or worse? Current performance may be good or poor. The direction over time can take several pathways to improved, stable, or degraded performance (Figure 1).
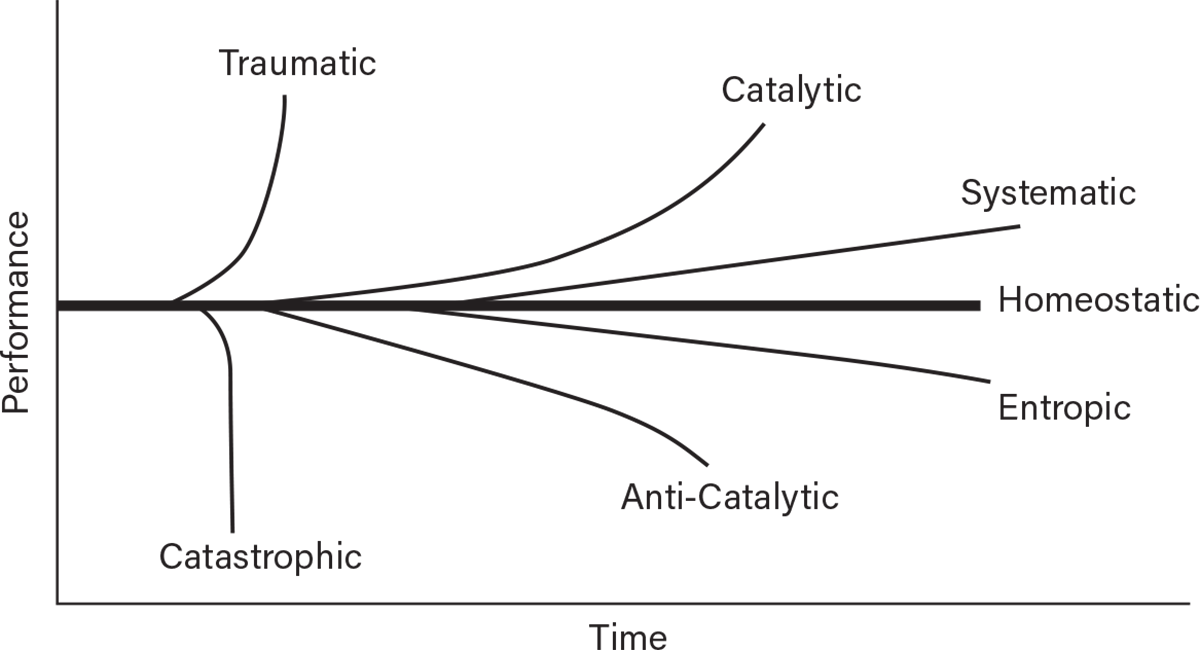
▲Figure 1. A facility’s process safety performance can change over time (3).
Entropic. A slow degradation of performance is most common when continued attention to process safety performance is not maintained, often resulting from complacency (e.g., lack of any recent significant incidents leads to confidence that performance is adequate), lack of awareness of degradation (e.g., poor measurement and feedback systems), or competing priorities (e.g., financial pressures). Performance may continue along this path until an event, such as an incident or audit, triggers a change of focus.
Homeostatic and systematic. Performance remains stable or steadily improves, based on continued goal setting and focus. Performance is likely to already be good so the intent is to continue to provide resources to appropriately manage process risks. If performance is not already good, then these scenarios may indicate more resources or management attention is needed to substantially improve performance.
Catalytic and anti-catalytic. Triggering events either lead to rapid improvement or degradation of performance. Typical trigger events may include: a near-miss event that raises awareness of possible performance issues; a change of leadership, such as a new plant manager with a different priority level for safety; an acquisition or merger, especially when there are significant differences in corporate safety culture; financial considerations due to a change in the economy or company cost control; a regulatory change or inspection; internal audits, inspections, or management visits that assess performance; or lawsuits or other legal considerations.
Traumatic and catastrophic. Significant, rapid performance changes typically result from serious incidents at a facility, company, or related industry. If a serious incident occurs at the facility, performance will drop immediately, and the disruption and distractions caused by the incident may lead to continued performance issues or even closure of the facility. If the serious incident occurs at another facility in the company or industry, it may serve as a wake-up call to motivate management to focus immediately on providing resources to implement or significantly improve process safety programs.
Companies must consider their current level of process safety performance and anticipate whether performance is likely to get better or worse. Addressing these two questions is essential for identifying improvement needs and for achieving or maintaining desired performance levels. This leads to a third question, which will be addressed in Part 2 in the April issue: 3. What can be done to achieve and/or maintain excellent performance?
Jim Klein, CCPSC, CPSA, is President of Process Safety Performance LLC (Email: jim.pspllc@gmail.com). He is a Fellow of both AIChE and CCPS.
- Klein, J., “Conservation of Energy, Conservation of Mass… and Conservation of Life?,” Chemical Engineering Progress, 117 (10), p. 46 (Oct. 2021).
- Klein, J. A., and B. K. Vaughen, “Process Safety: Key Concepts and Practical Approaches,” CRC Press, Boca Raton, FL (2017).
- Klein, J. A., “Sustaining Effective Process Safety Programs,” Chemical Engineering, pp. 24–29 (Feb. 2020).
- Klein, J. A., “Factors That Impact Safety Performance and How They Can Be Used to Achieve and Sustain Excellent Performance,” Professional Safety, pp. 48–52 (June 2021).
Copyright Permissions
Would you like to reuse content from CEP Magazine? It’s easy to request permission to reuse content. Simply click here to connect instantly to licensing services, where you can choose from a list of options regarding how you would like to reuse the desired content and complete the transaction.