This article is based on a presentation at the AIChE Spring Meeting, San Antonio, TX (March 2017).
When designing a liquid-liquid extraction column, pilot plant testing generates the data necessary for accurate scaleup to the production rate. This article describes how to optimize pilot plant testing.
Pilot plant testing is an integral part of designing a liquid-liquid extraction (LLE) column. Performing pilot plant testing with actual feed liquid, and then relying on known scale-up correlations to size the column, is one of the best and most reliable methods of determining the specific extraction column best suited for an application (1). In general, the design process consists of the following steps (2):
- Select the solvent and generate liquid-liquid equilibrium data.
- Use this information and the project requirements to select the column type.
- Perform a pilot plant test to generate the data for accurate scaleup to the production column.
- Design and fabricate the column.
This article focuses on optimizing the pilot plant testing methodology. During process development work, pilot plant testing is often hindered by several factors, which include:
- availability of the feed materials. Often, very little, if any, actual feed material is available.
- known purity of the solvent. Because the solvent is usually a recycle stream, the solvent will generally not be pure during actual commercial operation.
- time restraints. Often, testing must be done quickly to meet deadlines.
- disposal of waste materials. It is generally desirable to minimize the amount of waste material generated during pilot plant testing.
For those reasons, it is important to implement an optimized pilot plant testing method that can be completed in a short time frame using minimal amounts of feed and solvent. For basic research and development (R&D) work, experimental design is a well-proven and accurate method for process optimization. However, for pilot plant testing, experimental design requires significant amounts of feed and solvent and can take a long time.
This article presents a step-by-step method for pilot plant testing that saves both time and material. This method does require some experience, but when it is applied correctly, it can ensure that an extraction column is optimally designed and performs as required.
Laboratory work prior to pilot testing
Before pilot plant testing, the first step in developing an extraction process is selecting the solvent and generating equilibrium data (e.g., distribution coefficient vs. solute concentration). You can do this in several ways, one of which is outlined in Ref. 3.
In addition to obtaining raw equilibrium data, it is just as important to observe the phase behavior of the system, especially for selecting the right type of column for scaleup and developing a test plan for that column. When lab-testing the extraction process, gather the following pieces of data:
- mixing intensity required to generate good phase dispersion
- mass-transfer rate and the time required to reach equilibrium (we have learned that equilibrium can generally be reached in 2 min with high-speed mixing, except if one or both phases are viscous [>100 cP])
- after mixing, the time for the phases to separate and achieve a clear interface
- the interface behavior — is there a rag layer (of solids) or an emulsion band that forms at the interface?
- entrainment (i.e., discrete, undissolved droplets of one phase flowing out of the column with the other phase) — is some entrainment observed in one or both phases?
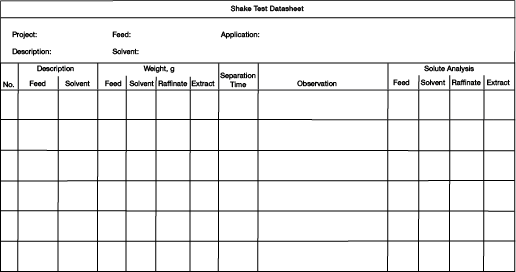
▲Figure 1. When performing lab tests for an extraction process, use a datasheet such as this to record liquid-liquid equilibrium data for each test.
A typical datasheet for generating liquid-liquid equilibrium data is shown in Figure 1. For each mix-decant cycle, the datasheet will provide the material balance, the solute concentration in both phases, and the observation of the phase behavior. These data will help you select the best extraction column for the process and serve as the starting point for pilot plant testing.
Pilot plant test method
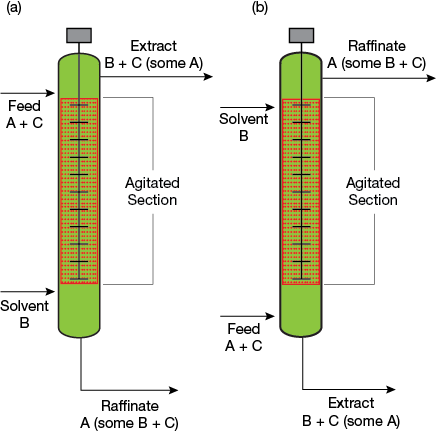
▲Figure 2. Agitated, counter-current extraction units can be set up in one of two ways. (a) When the solvent is lighter than the carrier liquid, the solvent is introduced at the bottom of the column and the solute is carried up toward the top of the extractor. (b) When the solvent is heavier than the carrier, the solvent is introduced at the top of the column and the solute is carried downward by the solvent toward the bottom of the column. The red dots represent the region in which the solute is transferred to the solvent.
This section presents the optimized method for pilot plant testing an agitated extraction column (Figure 2). Following this section, two examples illustrate how to use the method.
This method requires fairly quick analysis of the samples generated in the pilot column. The solute concentration in the raffinate is typically the key indicator of the column’s performance. It is also highly desirable to perform the test in a glass-shell extraction column so that the operators can observe the phase behavior and tweak the column operating conditions accordingly. The procedure is as follows:
- Select the continuous and dispersed phase for the process. In an extraction process, mass transfer occurs between the droplets (dispersed phase) and the surrounding liquid (continuous phase). Several factors can affect which phase is continuous and which phase is dispersed (a topic that is not covered in this article).
- Select the column for scaleup and then set up the pilot column with multiple inlets. If possible, it is best to set up a column that you expect to be taller than required. A manifold system can be included to vary the inlet location for the dispersed phase. The continuous phase must have a fixed entrance point.
- Select the initial operating conditions for the test. The height of the column, capacity, solvent-to-feed ratio, temperature, and initial agitation speed should all be established. This may be difficult to do unless you have some previous experience with similar extraction processes.
- Start up the column in the usual manner (4) and set a low agitation speed, which should be significantly below the flooding point of the process. Observing the phase behavior in the glass-shell column will help you determine this speed. Calculate the turnover time for the process (i.e., the volume of the column divided by the sum of the feed and the solvent flowrates). During the first two column turnovers, the agitation speed can be increased slightly if...
Would you like to access the complete CEP Article?
No problem. You just have to complete the following steps.
You have completed 0 of 2 steps.
-
Log in
You must be logged in to view this content. Log in now.
-
AIChE Membership
You must be an AIChE member to view this article. Join now.
Copyright Permissions
Would you like to reuse content from CEP Magazine? It’s easy to request permission to reuse content. Simply click here to connect instantly to licensing services, where you can choose from a list of options regarding how you would like to reuse the desired content and complete the transaction.