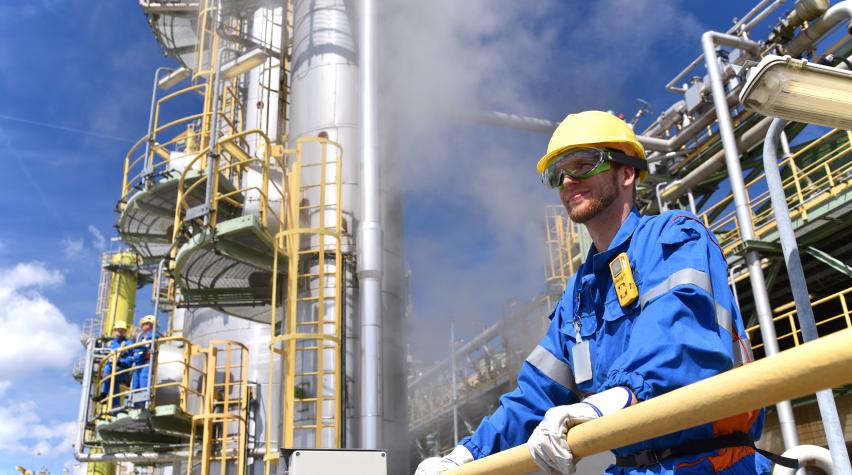
Part 1 – Traditional Process Engineering
Chemical engineering is perhaps the broadest field of engineering, and it introduces a person to a life-long approach to analytical thinking, trouble-shooting, and problem-solving. With a focus on making more useful outputs from a set of inputs, chemical engineers also combine molecular and mechanical knowledge to large-scale production environments.
When I graduated from high school, I had no idea what I wanted to do “when I grew up.” Thanks to the wisdom of my high school chemistry teacher, I enrolled in the chemical engineering program at University of Idaho. I loved learning more math, chemistry, and even physics. But I still was not quite sure what, exactly, chemical engineers did. I hope this series of articles on the broad spectrum of careers that a ChE degree opens will help you understand what it means to be a chemical engineer.
Process engineering
Traditionally, chemical engineers have worked as process engineers in refineries and chemical plants. We understand “the process” and monitor the conversion of less valuable inputs to desirable consumer outputs. Of course, oil is valuable, but “mogas” and jet fuel are even more desired and useful. (“Mogas” is short for motor gasoline, consumed by most automobiles and composed primarily of octane molecules.)
Working at a plant, chemical engineers monitor operations to keep things running effectively and efficiently. On a daily basis, a process engineer will check data, such as unit temperatures and pressures, relayed by the plant computer control system. Process engineers work closely with the analytical labs to ensure samples are within expected ranges to maintain product quality.
These tasks require excellence in technical skills, such as mathematical and statistical trending, understanding chemistry, and an in-depth knowledge of the unit’s process flow and equipment (e.g., reactors, distillation, furnaces, and so on). Process engineers spend a great deal of time in the plant, so adhering to safety rules is a must. Communication skills are also important as process engineers work with operators, technicians, and other functional engineers (such as rotating equipment, electrical, civil, and so on). Additionally, process engineers provide status reports and presentations to plant management to verify production and manufacturing conditions.
Design engineers
In contrast to process engineers, design engineers spend a good portion of their day in front of computers, doing calculations. Design engineers often work for EPC companies (engineering, procurement, and construction) who provide services to major refiners and chemical producers. Note that all major petrochemical companies also have some in-house design staff, but most engineering design is done through specialized contractors. This allows operating plants to save money by utilizing experts on a temporary basis.
Chemical engineers employed at design firms work on the flow sheets and layout of equipment. Design engineers must be familiar with both creating and running models that simulate plant operations. Therefore, a deep understanding of chemical reactions, kinetics, heat transfer, and fluid flow is key to success. Often, design engineers work with process engineers to improve yield or throughput. Close alignment with plant personnel is also necessary when designing and building a new plant or process. It is not uncommon for chemical engineers to start their career as process engineers and transition to design engineering, applying field knowledge for long-term operational improvements.
Plant support
In future articles, we will discuss some of the more specialized career paths of chemical engineers, such as quality and project management. However, traditional petrochemical jobs also include plant support, such as reliability, environmental, and safety. ChEs working in safety, for example, evaluate both designs and operating systems to minimize the inherent hazards of working with chemicals. Safety engineers learn about special devices to prevent incidents and provide expertise to manage risks in an operating unit. They also monitor databases of incidents at other facilities that may impact compliance with new safety regulations.
Environmental and reliability engineers complement the role of the safety engineer. Environmental engineers (sometimes with degrees in civil or environmental engineering) also monitor compliance with legislation and regulations. The goal is to prevent undesirable releases to the air, water, or soil. Similarly, reliability engineers strive to keep the plant operating at production scale to minimize costs and maximize profit. In these plant support roles, chemical engineers are exposed to many different roles and responsibilities yet must also have a deep understanding of the process and flow at the facilities where they work.
Traditional career paths for ChEs
A great percentage of chemical engineers work in traditional process and plant support roles, including design. These types of jobs utilize much of the knowledge gained in a mainstream chemical engineering university program, such as reaction kinetics, thermodynamics, and mass transfer. Successful process and design engineers take advantage of field knowledge by learning how a specific plant or unit operation functions in detail. Many operating petrochemical facilities utilize the broad analytical and trouble-shooting skills of chemical engineers in other important roles, such as safety, environmental, and reliability.
In our next article, we’ll discuss the very broad field of R&D and how chemical engineers are uniquely suited for careers in innovation.
If you are interested in learning more about professional development, networking, and interviewing, be sure to check AIChE Career DiscoveryTM, which is part of the Institute for Learning & Innovation (ILI). See upcoming instances of the Career Discovery Workshop on AIChE Academy and read more about the process here.
Learn more about professional development