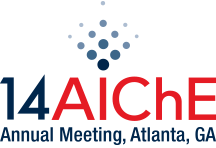
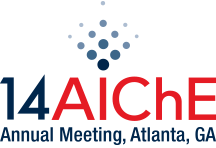
It is highly desired to implement a closed-loop feedback control system into a pharmaceutical manufacturing plant to enable the transition toward a more desirable Quality by Design (QbD), rather than Quality by Testing (QbT) based manufacturing of the next generation of pharmaceutical products. This approach utilizes an optimal utilization of resources, while satisfying the strict regulatory constraints, flexible market demands, operational complexities, and economic limitations.
In different industrial sectors such as chemical and petrochemical a closed-loop control process operations has proven to be a very effective operational strategy over the last 30 years [1]. Hoverer, in comparison to classical control schemes (PID), Model Predictive Control (MPC) is more complex to implement and is computationally more expensive. Therefore, a hybrid strategy that takes advantage of both MPC and PID is an optimal alternative for pharmaceutical manufacturing. The control hardware, software and sensor integration and thereby implementation of an advanced control system into the actual pharmaceutical pilot-plant for efficient closed-loop operation is still a challenging task because of different level of complexities (e.g. solid handling) involved [2].
In this work, a plant-wide advanced hybrid MPC-PID control system has been implemented into direct compaction continuous tablet manufacturing pilot-plant. The critical control variables includes, drug concentration, powder level in an instrumented hopper, tablet weight and hardness. The control loops have been closed using industry standard control platform (e.g. DeltaV), PAT data management tool (synTQ), OPC communication protocol and fieldbus devises. For drug concentration control, PAT system is used to read the NIR spectral data at blender outlet and communicate it to the MVA (Multi-Variable Analysis) model performing PCA/PLS to provide the API concentration.
A chemometric tool is used for real time NIR prediction and a PAT data management tool is used to manage the process data and to send the signal to the control platform using OPC communication protocol. The instrumented hopper level (placed in between blender and tablet press) is controlled by manipulating the speed of a rotary valve. The hopper level is monitored by webcam. The webcam takes the image of powder level in real time and passes it to the MATLAB image analysis toolbox where the actual powder level has been calculated. The measured level is then sent to control platform via MATLAB OPC toolbox as the input to MPC block.
In the tablet press, the tablet weight and hardness are controlled through a cascade control arrangement using two master loops and one slave loop. Master loops are used to control the weight and hardness and provide the set point for the slave controller, which controls the main compression force by manipulating the fill depth. They share a common slave controller, meaning that only one master controller is activated at a time. The tablet weight is measured and controlled more frequently than hardness. Check master (Fette) has been used for tablet weight and hardness measurement in real time.
The main challenges in this implementation are the integration of multiple hardware/software platforms including Process Control System, NIR analyzer, Multi-Variable Analysis (MVA) software, Process Modeling Software, and Bus Technology. The performance of hybrid MPC-PID scheme has been compared with cascade PID and cascade PID with Smith predictor schemes. Results demonstrate enhanced performance of critical quality attributes (CQAs) under hybrid MPC-PID scheme compared to cascade PID/Smith predictor schemes, thus illustrating the potential of hybrid MPC-PID control system in improving pharmaceutical manufacturing operations.
The objective of this presentation is two-fold. First to highlight the plant-wide implementation of hybrid MPC-PID control system into a continuous tablet manufacturing pilot-plant, and second to demonstrate the performance of the implemented control system.
[1]. Singh, R., Ierapetritou, M., Ramachandran, R. (2013). European Journal of Pharmaceutics and Biopharmaceutics, 85, 1164–1182. 1.
[2]. Singh, R., Abhishek Sahay, A., Muzzio, F., Ierapetritou, M., Ramachandran, R. (2014). Computers & Chemical Engineering, DOI: 10.1016/j.compchemeng.2014.02.029.