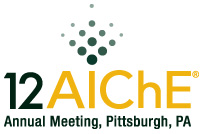
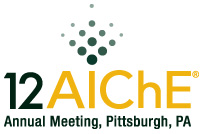
Filter drying, also referred to as vacuum contact drying, is a process widely used in the pharmaceutical industry to remove water or organic solvents. The advantage of this process over other drying operations is that it can be used to dry solids that are sensitive to oxygen and temperature.
The entire drying process is typically carried out in two stages in a vessel. Typically a cylindrical vessel is used although conical vessels are also encountered. In the first blowdown stage, pressure in the form of nitrogen is applied to remove excess solvent by convective drying. At the end of this stage, the wet filter cake typically has around 45% solvent on a wet basis.
The second, longer, period involves heating the walls of the filter cake while vacuum is applied to dry the cake to about 1% to 0.1%. During this stage, heat conduction from the wall to the interior of the cake is often the rate limiting step. While the process can be carried out without agitating the bed, this can lead to excessively long drying times and heterogeneity of the cake. On the other hand, continuous long agitation often results in agglomeration and/or breakage of the solid. As a compromise, intermittent periods of agitation are carried out to redistribute solvent and heat, resulting in faster drying times but without significant agglomeration and/or breakage of solid taking place.
A detailed model of the filter dryer unit operation has previously been published in the literature (Murru et al, 2011). The key features of the model are:
1. The second drying phase is modelled and drying is assumed to take place primarily due to heat conduction from the equipment walls. The blowdown phase where convective drying takes place is not accounted for.
2. A single solvent is considered. This allowed for process optimisation by allowing different solvents to be examined for the effects on total drying times.
The model was successfully used to predict drying times for various equipment sizes and solvents at both pilot plant and manufacturing scales.
In this work, the model is further extended to consider the following phemonena.
1. Convective drying is considered. This allows the modelling of the initial blowdown drying phase. The effects of the applied suction during the second drying phase are also explicitly accounted for. The application of hot nitrogen flow over the bed can significantly reduce the time of drying.
2. The model is extended to non-ideal mixtures of solvents. The presence of solvent mixtures in the drying operation has a significant effect on the drying time but most importantly lead to change of composition of the residual solvent during drying. This can lead to stability issues (hydrates / solvates) or can lead to particle bridging and agglomeration. Understanding the dynamics of the solvent composition is crucial to avoid these situations. The ability to handle multiple solvents simultaneously will allow for greater flexibility in selecting solvents for process optimisation.
3. Modelling of the vapour processing step is undertaken. This allows for data from downstream condensation and scrubbing unit operations to be used in model validation.
References
M Murru, G Giorgio, S Montomoli, F Ricard, F Stepanek (2011) Model-based scale-up of vacuum contact drying of pharmaceutical compounds. Chemical Engineering Science 66, 5045-5054